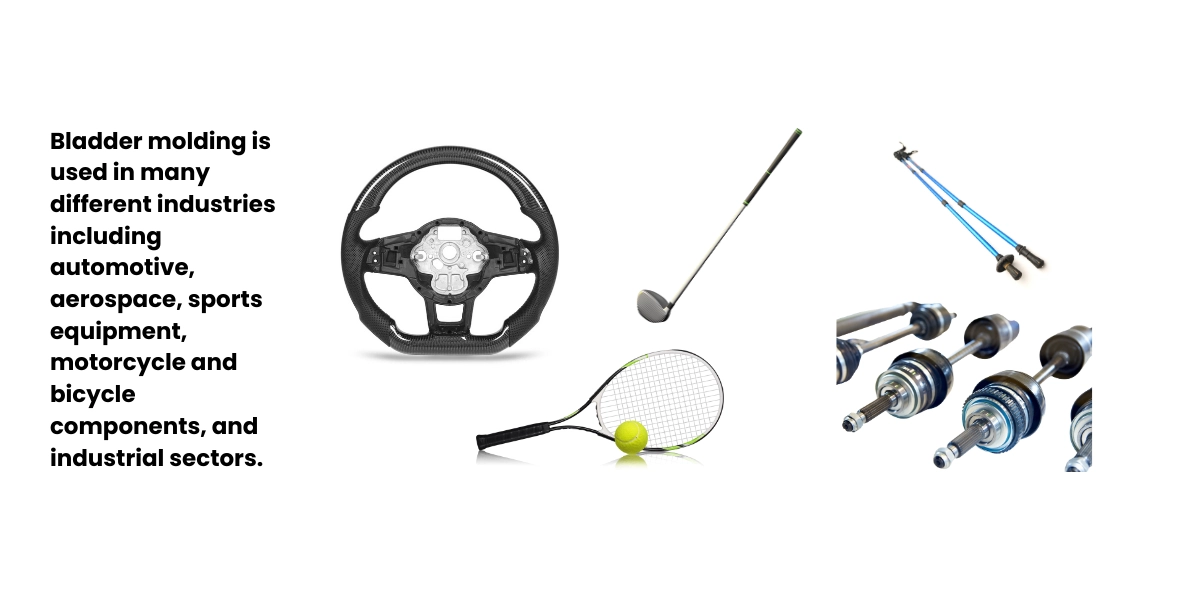
- Blog
- 25 Mar 2025
Bladder Molding Process for Composite Industry
The bladder molding process is a widely used technique in the composite manufacturing processes industry, known for its ability to produce complex, high-strength parts with precision. This method is especially popular in creating hollow or intricate composite structures that are difficult to achieve with traditional molding techniques. By using an inflatable bladder inside a mold, manufacturers can apply uniform pressure to shape materials like carbon fiber supplements into durable and lightweight components. As demand for advanced composites grows across industries such as aerospace, automotive, and sports equipment, understanding the best practices for the bladder molding process becomes essential for achieving high-quality results, improving efficiency, and reducing production costs.
What is the Bladder Molding Process?
The bladder molding process is an advanced technique used in composite manufacturing processes to create hollow or complex-shaped composite parts. It involves placing an inflatable bladder inside a mold, around which composite materials—often reinforced with carbon fiber supplements—are laid. Once the materials are positioned, the mold is closed, and the bladder is inflated, applying internal pressure. This pressure forces the composite material against the mold walls, ensuring it takes the exact shape and forms a strong, uniform structure.
To assist in the release of the finished part, mold release agents are applied to the mold’s interior before the process begins. These agents prevent the composite material from sticking, making it easier to remove the final product without damage. The mold is then subjected to controlled heat and pressure, often using specialized composite machines, to cure the materials, solidifying them into a durable and lightweight component.
The bladder molding process is valued for its precision and versatility, making it ideal for producing complex parts such as aerospace components, automotive structures, and high-performance sporting goods. Its ability to create seamless, hollow designs with excellent strength-to-weight ratios sets it apart from other composite molding techniques.
Benefits of the Bladder Molding Process in the Composite Industry
The bladder molding process offers significant advantages in composite manufacturing processes, making it a preferred method in industries like aerospace, automotive, and sports equipment. Its ability to create complex, hollow shapes provides greater design flexibility compared to traditional molding techniques. By using materials such as carbon fiber supplements, it produces lightweight yet durable components with an excellent strength-to-weight ratio.
The process ensures consistent quality, as the internal pressure from the bladder distributes the material evenly, reducing voids and imperfections. The use of mold release agents also helps achieve smooth surfaces and easy part removal. Additionally, bladder molding is cost-effective, as it minimizes material waste and reduces the need for extensive post-processing. Its versatility in handling different composite materials makes it ideal for a wide range of applications, further solidifying its role in modern composite manufacturing.
Bladder Molding Process Best Practices
Applying best practices in the bladder molding process is essential to achieve high-quality, durable composite parts. From selecting the right materials to maintaining precise control over pressure and temperature, each step plays a critical role in ensuring consistent results. Following these guidelines not only improves product performance but also enhances efficiency and reduces production costs in composite manufacturing processes.
Material Selection and Preparation
Choosing the right composite materials is crucial for a successful bladder molding. High-quality fibers like carbon fiber supplements and compatible resins ensure strength and durability. Materials should be clean, dry, and properly cut to fit the mold, while applying mold release agents helps prevent sticking and ensures smooth part removal.
Proper Bladder Inflation Control
Controlling bladder inflation is key to achieving uniform pressure. Over-inflation can cause defects, while under-inflation may lead to incomplete part formation. Monitoring inflation levels throughout the process helps maintain consistency and part integrity.
Optimal Temperature and Pressure Management
Accurate temperature and pressure control during curing is essential. Using calibrated composite machines ensures even heat distribution and proper resin flow, leading to fully cured, high-quality parts without warping or voids.
Quality Control and Inspection Tips
Regular inspections help maintain product quality. Check for voids, wrinkles, or surface defects after demolding. Dimensional accuracy should also be verified to ensure parts meet specifications. Consistent quality checks reduce errors and improve overall process efficiency.
Applications of Bladder Molding in the Composite Industry
The bladder molding is widely used across various industries due to its ability to produce complex, lightweight, and durable composite parts. In the aerospace sector, it’s commonly used to manufacture hollow components like ducts, fairings, and control rods, where strength and weight reduction are critical. The automotive industry also benefits from this process, especially for producing lightweight structural parts, drive shafts, and performance-enhancing elements made with carbon fiber supplements to improve fuel efficiency and vehicle dynamics.
In the sports and recreation sector, bladder molding is used to create high-performance equipment such as bicycle frames, golf club shafts, and hockey sticks, where precision and strength-to-weight ratios are essential. It also plays a role in medical and industrial applications, producing durable tubing and structural components. Thanks to its versatility and ability to handle complex shapes, the bladder molding process continues to be a key technique in modern composite manufacturing processes.
The bladder molding process has become a vital technique in the composite manufacturing processes industry, offering the flexibility to produce complex, lightweight, and durable parts across various sectors. By following best practices—such as proper material selection, precise bladder inflation, and controlled temperature and pressure—manufacturers can ensure high-quality results while improving efficiency and reducing costs. With its wide range of applications, from aerospace components to sports equipment, and the ability to work with advanced materials like carbon fiber supplements, the bladder molding process continues to drive innovation and performance in composite production.