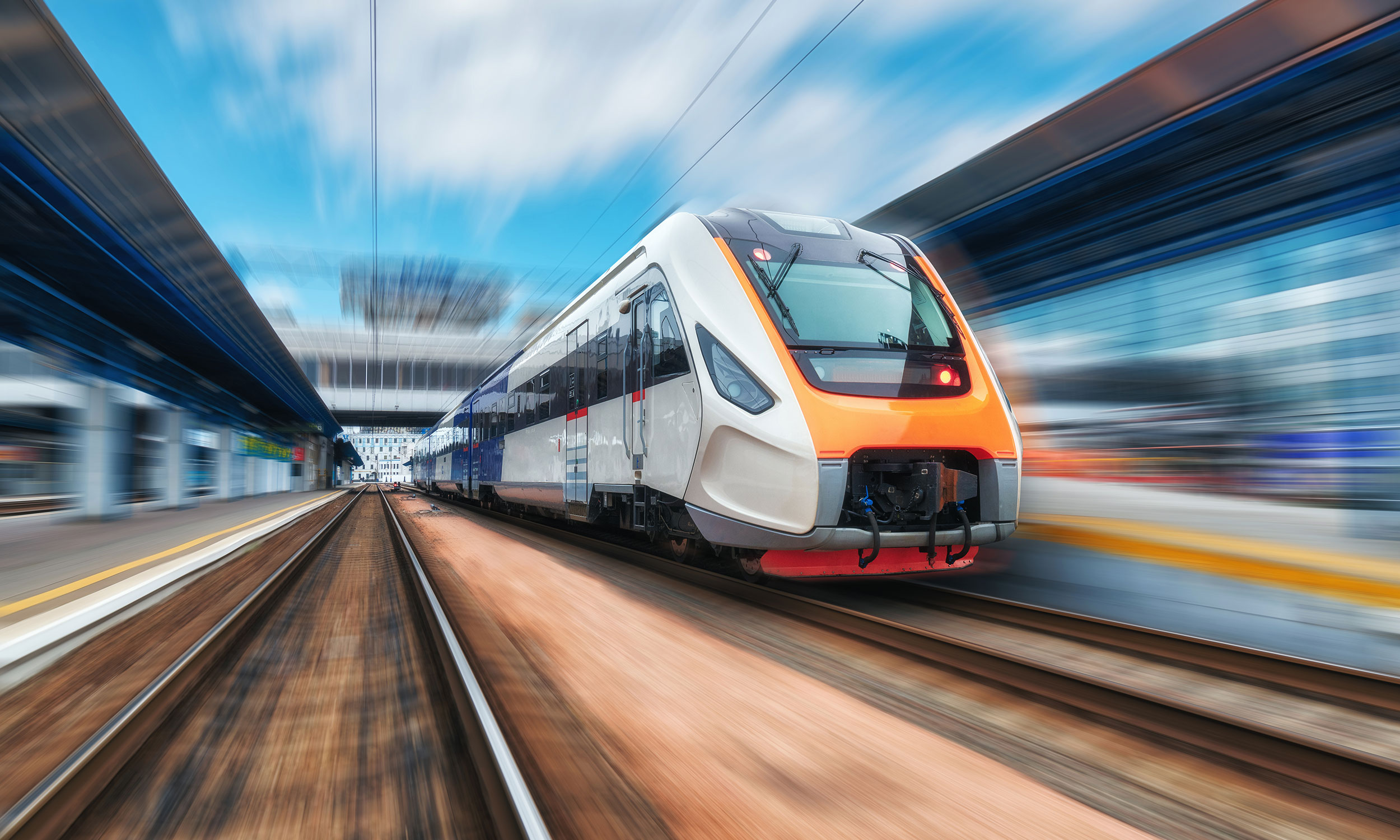
Vehicles and Transportation
The automotive industry has experienced a significant transformation in recent years, driven by the widespread adoption of composite materials in vehicle manufacturing. Composites, which are created by combining two or more distinct components such as fibers and resins, offer a range of unique properties that make them ideal for various automotive applications.
Composites have revolutionized the automotive industry, providing improved performance, increased fuel efficiency, and enhanced safety features. With their exceptional strength-to-weight ratios, composite materials offer manufacturers the opportunity to design lighter vehicles without compromising on strength and durability. This shift towards composites in automotive manufacturing is reshaping vehicle design and performance metrics.
Types of Composites Used in Vehicle Manufacturing
There are several types of composites used in vehicle manufacturing, each offering distinct characteristics and advantages for specific automotive applications. Some commonly used composites include:
Carbon Fiber Reinforced Plastics
Carbon fiber reinforced plastics (CFRP) are a popular choice in the automotive industry due to their exceptional strength-to-weight ratio. These composites are created by combining incredibly thin, strong, and lightweight carbon fibers with a resin matrix. CFRP materials offer high stiffness, low density, and excellent fatigue resistance. As a result, CFRP composites are commonly used in high-performance sports cars and luxury vehicles to improve performance and reduce weight. The role of CFRP as composites in automotive design underscores their significance in pushing the boundaries of vehicle performance and efficiency.
Glass Fiber Reinforced Plastics
Glass fiber reinforced plastics (GFRP) are widely used in automotive applications due to their affordability, versatility, and impact resistance. GFRP composites are made by combining glass fibers with a matrix, typically a polyester resin. These composites provide good mechanical properties, corrosion resistance, and are relatively easy to manufacture. GFRP is commonly used in the construction of body panels, bumpers, and interior components in vehicles. The incorporation of GFRP as composites in automotive construction highlights their importance in enhancing vehicle safety, durability, and cost-efficiency.
Natural Fiber Composites
Natural fiber composites are gaining popularity in the automotive industry due to their eco-friendly and sustainable nature. These composites are made by combining natural fibers, such as hemp, flax, or sisal, with a resin matrix. Natural fiber composites offer advantages such as weight reduction, energy absorption, and vibration damping. They are being used in interior trims, door panels, and other non-structural components to reduce the environmental impact of vehicle manufacturing. The utilization of natural fiber composites in automotive manufacturing is a testament to the industry’s commitment to sustainability and environmental responsibility.
Advantages of Using Composites in Automotive Applications
Composites offer numerous advantages when used in automotive applications, contributing to improved vehicle performance, fuel efficiency, and durability.
Weight Reduction and Fuel Efficiency
One of the key advantages of using composites, especially lightweight composites like carbon fiber reinforced plastics, in automotive manufacturing is the significant reduction in weight compared to traditional steel or aluminum materials. By replacing heavy metal components with lightweight composites, vehicles become lighter, resulting in improved fuel efficiency and reduced emissions. This weight reduction not only enhances the overall energy efficiency of the vehicle but also helps manufacturers meet stricter fuel economy standards and reduce their carbon footprint. The incorporation of composites in automotive design thus marks a pivotal shift towards more sustainable and efficient vehicle construction.
Enhanced Strength and Durability
Composites, particularly high strength composites like carbon fiber composites, offer excellent strength-to-weight ratios, making them ideal for structural applications in vehicles. These materials provide exceptional strength and stiffness, allowing manufacturers to design safer and more crash-resistant vehicles. Additionally, composites exhibit good impact resistance, reducing the risk of deformation or damage in the event of accidents. With their inherent durability, composites contribute to the longevity and reliability of automotive components, ensuring a long-lasting vehicle. The role of composites in automotive safety and durability underscores their critical importance in modern vehicle manufacturing.
Corrosion Resistance
Unlike metals, composites are inherently resistant to corrosion, making them ideal for automotive applications, especially in corrosive environments. Traditional metal components are susceptible to rust and degradation over time, particularly in regions with harsh weather conditions. By using corrosion-resistant composites, manufacturers can improve the lifespan of automotive components, reduce maintenance costs, and enhance the overall durability of the vehicle. These corrosion-resistant composites in automotive design provide effective rust prevention, ensuring that the vehicle remains in excellent condition for an extended period.
Challenges and Considerations in Adopting Automotive Composites
While the use of composites in automotive manufacturing offers numerous advantages, there are several challenges and considerations that need to be addressed.
1. Manufacturing Costs:
The manufacturing costs of composites can be higher compared to traditional materials such as steel or aluminum. The production processes involved in creating composites often require specialized equipment and skilled labor, resulting in increased expenses. Additionally, the cost of raw materials used in composites, such as carbon fibers or resins, can be higher than conventional materials. Manufacturers need to carefully evaluate the economic viability of using composites in automotive manufacturing processes.
2. Design Complexity:
The design complexity of composites can pose challenges in the manufacturing process. Composites offer the flexibility to create complex shapes and geometries, but this can also increase the complexity of tooling and molding. Ensuring proper alignment of fibers, minimizing voids or defects, and achieving consistent part dimensions require precise engineering and manufacturing techniques. Dealing with these complexities may require additional time, resources, and expertise in the design and manufacturing stages of composites in automotive applications.
3. Repairability:
Repairing composites can be more challenging compared to traditional materials. While composites offer high strength and durability, they can suffer damage in the event of impacts or accidents. Repairing composites often requires specialized knowledge and techniques to restore the structural integrity and appearance of the damaged parts. Additionally, the repair process may involve lengthy curing times or require specific tools and equipment, impacting the downtime and cost of repairs. The challenges of repairing composites in automotive contexts highlight the need for specialized training and resources.
In conclusion, while composites offer numerous advantages in automotive manufacturing, addressing challenges related to manufacturing costs, design complexity, and repairability is essential for successful adoption. Manufacturers must carefully evaluate the economic feasibility, invest in research and development, and develop expertise in working with composites in automotive applications to optimize their benefits.
Design Innovations with Composites in Automotive
Integrated Structures and Body Panels
Composites, particularly carbon fiber reinforced plastics, have revolutionized vehicle design by enabling the integration of structural components within the vehicle’s body panels. This innovative monocoque construction method eliminates the need for separate chassis frames, resulting in lightweight designs with improved strength and rigidity. By integrating structural components, manufacturers can optimize vehicle performance while reducing weight, leading to enhanced fuel efficiency and agility on the road. The role of composites in automotive construction is critical in achieving these advancements.
Aerodynamic Enhancements
Composites offer unrivaled design flexibility, allowing manufacturers to create complex shapes and aerodynamic profiles that minimize drag and enhance vehicle performance. By utilizing the moldability of composites in automotive designs, automotive designers can craft sleek, streamlined exteriors that reduce air resistance and improve fuel efficiency. Through meticulous wind tunnel testing and computer simulations, the aerodynamic properties of composite components can be fine-tuned to achieve optimal performance and maximize the vehicle’s potential.
Design Flexibility for Aesthetics
Composites provide unparalleled design flexibility, enabling manufacturers to create visually stunning and unique vehicle designs. The moldable nature of composites allows for the creation of complex curves, sharp angles, and innovative aesthetics that are not easily achievable with traditional materials. This design freedom empowers automotive brands to differentiate themselves in the market and create vehicles that showcase their unique identity and brand DNA. Customizable designs made possible by composites in automotive ensure that every vehicle exudes a distinct character, captivating the hearts of consumers who value individuality and style.
Manufacturing Processes for Automotive Composites
Several manufacturing processes are utilized in the production of automotive composites, each with its own advantages and applications.
Resin Transfer Molding (RTM)
Resin transfer molding (RTM) involves infusing liquid resin into a preform containing fibers or fabric. The resin is injected under pressure to impregnate the fibers, and the composite is then cured to achieve the desired properties. RTM is suitable for creating complex shapes and can be used for high-volume production. It offers good dimensional stability, high fiber volume fraction, and excellent surface finish.
Compression Molding
Compression molding involves placing dry fibers or fabric in a mold and applying heat and pressure to shape the composite. Sheet molding compound (SMC) is a common material used in compression molding, consisting of resin, filler, and reinforcing fibers. This process is cost-effective and ideal for large-scale production. Compression molding can create parts with good surface finish, dimensional accuracy, and excellent mechanical properties.
Injection Molding
Injection molding involves melting and injecting thermoplastic composites into a mold under high pressure. The molten composite material solidifies within the mold, taking its shape. Injection molding offers fast production cycles, making it suitable for automotive components with high production volumes. This process allows for the production of complex geometries and can incorporate various reinforcing fibers for improved mechanical properties.
Future Trends: Composites and the Automotive Landscape
The automotive industry is poised for significant transformations in the coming years, driven by emerging trends and developments in composite materials. These innovations will shape the future of composites in the automotive landscape, offering new possibilities for electric vehicles (EVs), advancements in material strength, and the influence of government regulations and incentives.
Electric Vehicles and Composites
The rise of electric vehicles (EVs) has propelled the demand for lightweight materials to maximize battery range and efficiency. Composites in automotive will play a crucial role in meeting these objectives, thanks to their inherent lightweight nature. By integrating composite structures, manufacturers can offset the weight of EV batteries and enhance overall vehicle performance. Moreover, composites align with the sustainability goals of EV manufacturing, as they can be produced using bio-based materials and have a lower carbon footprint compared to traditional materials.
Advancements in Composite Materials
Ongoing advancements in composite materials continue to push their adoption in the automotive industry. Researchers and manufacturers are constantly exploring ways to enhance the strength and durability of composites in automotive, enabling them to withstand higher loads and impacts. Simultaneously, efforts are being made to reduce the overall cost of composite manufacturing, making them more economically viable for mass production. Recycling technologies are also being developed to improve the recyclability of composites, further enhancing their sustainability credentials and environmental impact.
Government Regulations and Incentives
Government regulations and incentives will shape the future of composites in the automotive industry. Stricter emission standards and fuel efficiency requirements are driving the adoption of lightweight composites as a means to reduce vehicle weight and improve efficiency. Governments may also provide incentives and support for the use of sustainable materials in vehicle manufacturing, promoting the adoption of composites with lower environmental impacts. These regulations and incentives will likely accelerate the integration of composites into the automotive landscape, pushing manufacturers to embrace sustainable materials and practices.