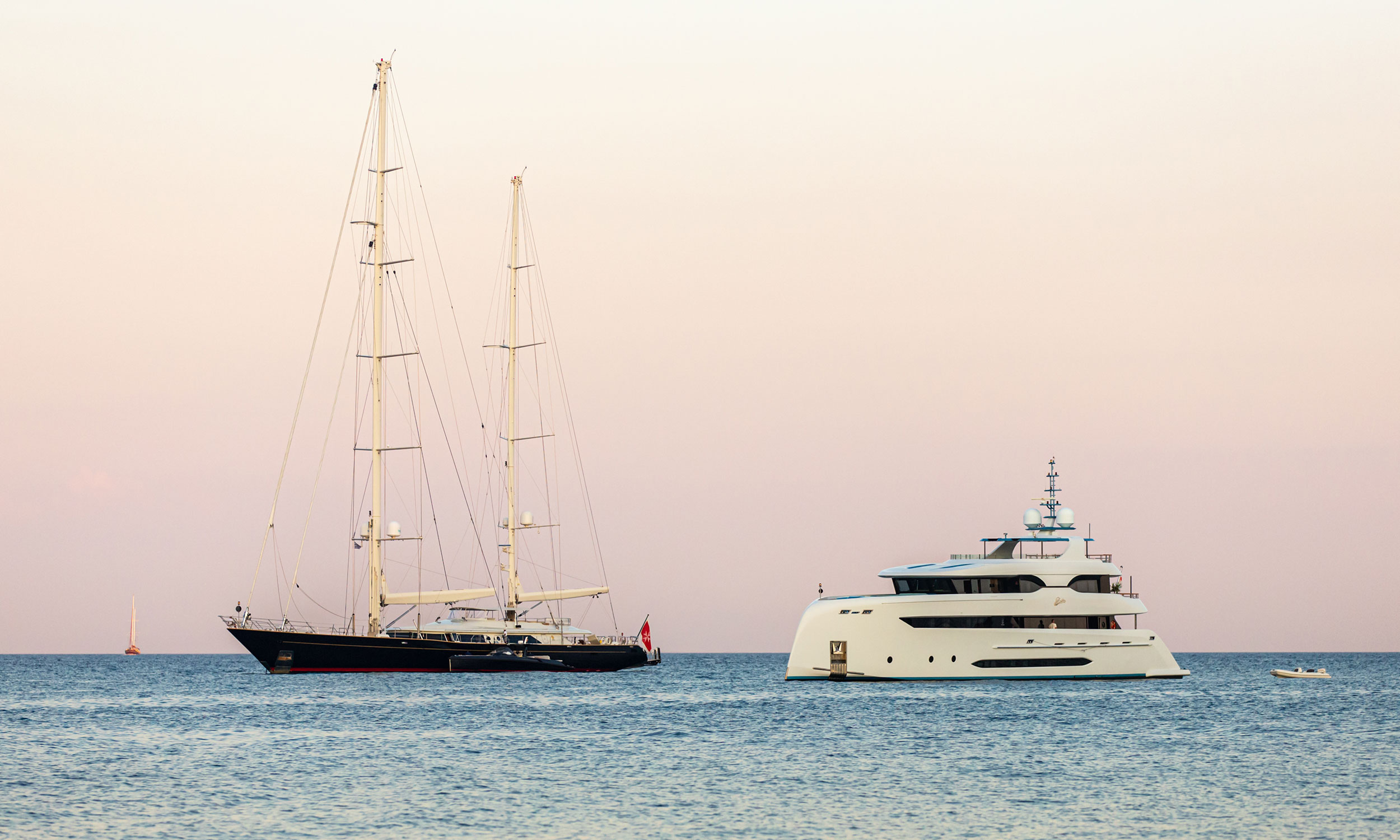
Marine
Marine composites have revolutionized the boat building industry, offering a superior alternative to traditional materials like wood and steel. With remarkable properties such as enhanced durability, lightweight construction, and corrosion resistance, these materials have become the go-to choice for boat builders.
Exploring the Advantages of Marine Composite Materials
The advent of advanced marine composites has sparked a paradigm shift in the fabrication of maritime vessels and structures. Recognizing the pivotal role these materials play, the industry has been quick to adopt them for their manifold benefits, ensuring enhanced functionality and resilience in marine applications.
Enhanced Durability in Harsh Marine Environments
Among the foremost advantages of marine composites is their exceptional durability. Designed to withstand the relentless challenges presented by the marine environment—be it the unrelenting UV radiation, the corrosive nature of saltwater, or the extreme flux in temperatures—these materials are a testament to innovation in marine construction materials. The ruggedness of advanced marine composites directly translates to an extended lifespan for vessels, making them an economical choice in the long run.
Lightweight Properties for Improved Vessel Performance
Performance is paramount in marine navigation, and lightweight boats have a distinct edge. With the deployment of lightweight composite materials in their construction, vessels gain significantly in terms of speed and fuel efficiency. This reduction in weight does not compromise strength; on the contrary, these composites are often stronger than traditional building materials, enabling boats to achieve better performance with less power.
Corrosion Resistance and Longevity
The resistance to corrosion is yet another feather in the cap for marine composites. This quality not only imparts longevity to marine crafts but also diminishes the need for frequent and costly maintenance. With marine construction materials being subjected to a marine milieu that can accelerate degradation, the corrosion resistance imbued by marine composites offers peace of mind, assuring a steady decrease in lifetime costs and resource demands. Thus, the complete picture that emerges is one of enduring and cost-effective marine engineering—realizable thanks to the extraordinary virtues of advanced marine composites.
Types of Marine Composite Materials and Their Applications
Boat building has greatly benefited from the use of marine composite materials. There are several types of marine composites commonly used in the industry, each offering unique properties and applications.
- Fiberglass Reinforced Plastic (FRP): FRP composites, also known as fiberglass composites, are widely used in boat building due to their durability, lightweight nature, and corrosion resistance. These composites consist of a matrix of polyester or epoxy resin reinforced with fiberglass. FRP composites are commonly used in vessels such as pleasure boats, fishing boats, and yachts.
- Carbon Fiber Reinforced Polymer (CFRP): CFRP composites are known for their exceptional strength and stiffness, combined with a lightweight structure. These composites are made by embedding carbon fiber sheets or fabric in a polymer resin matrix, usually epoxy. CFRP composites have found applications in high-performance boats, racing yachts, and luxury marine vessels.
- Kevlar Reinforced Polymer (KRP): Kevlar is a high-strength synthetic fiber known for its excellent impact resistance and toughness. KRP composites, which consist of Kevlar fabric embedded in a polymer resin matrix, offer enhanced protection against impacts and abrasion. These composites are commonly used in military and defense boats, as well as high-speed powerboats.
- Hybrid Composites: Hybrid composites are a combination of different types of reinforcement materials, such as carbon fiber, fiberglass, Kevlar, and even natural fibers like flax or hemp. By combining different materials, hybrid composites can offer a balance of properties tailored to specific applications. This flexibility makes them suitable for various boat types, including sailboats, catamarans, and commercial vessels.
- Marine Grade Plywood: Although technically not a composite material, marine grade plywood is often used in boat building due to its high water resistance and structural integrity. Marine plywood is made from thin layers of wood veneer bonded together with waterproof adhesive, making it suitable for decks, hulls, and interiors of boats.
These marine composite materials are chosen based on the specific requirements of the boat design, taking into account factors such as strength, weight, cost, and practicality. The selection of the appropriate composite material plays a crucial role in achieving optimal boat performance and longevity.
Manufacturing Processes for Marine Composites
When it comes to boat building, marine composites are a popular choice due to their exceptional strength, durability, and lightweight properties. The manufacturing processes used to produce these advanced materials are crucial in achieving the desired characteristics required for marine applications.
Vacuum Infusion Technique
Vacuum infusion stands at the forefront of marine composite manufacturing, ensuring a high fiber-to-resin ratio and uniform laminate consolidation. This technique leverages vacuum pressure to draw resin into a dry fiber layup placed within a mold, permeating the complex arrangements of fibers without the introduction of air bubbles. The method’s precision facilitates the development of marine components with consistent material properties and superior load-bearing capabilities, critical for vessels traversing the formidable ocean environment.
Hand Lay-up Method
Resilient in its simplicity, the hand lay-up method has been a cornerstone in the field of composite fabrication techniques. Artisans carefully arrange layers of fiber-reinforced materials, meticulously saturating them with a resin mixture by hand. The direct contact permits unparalleled adaptability and is especially effective for crafting unique, one-of-a-kind marine components. This approach remains indispensable for customized or low-volume production, where the human touch translates into fine craftsmanship within the marine composite domain.
Resin Transfer Molding (RTM)
Completing the trio, Resin Transfer Molding (RTM) presents a more automated approach to composite manufacturing. In this process, a pre-formed fiber-reinforced mat is placed between two mold halves. Resin is then injected under pressure, achieving a well-controlled resin-to-fiber ratio and enabling the production of complex shapes with smooth surfaces on all sides. RTM has gained traction for its ability to produce high volumes of marine components while maintaining consistency, structural integrity, and an enhanced surface finish suitable for the sleek designs prevalent in contemporary boat manufacturing.
The Role of Marine Composite in Modern Boatbuilding
Playing a significant role in the construction of modern boats, these materials have exceptional properties and advantages, making them the material of choice for many builders.
One of the key reasons for their wide use in boatbuilding is their lightweight nature. Compared to traditional materials, they offer a significantly lower weight-to-strength ratio. This not only improves the performance and maneuverability of boats but also enhances fuel efficiency.
In addition to their lightweight properties, they exhibit excellent durability. Resistant to corrosion, moisture, and UV exposure, they are ideal for withstanding the marine environment. This durability ensures that boats built have a longer lifespan, reducing the need for frequent repairs and maintenance.
Furthermore, marine composite materials provide boat builders with greater design flexibility and versatility. They can be molded into various shapes and sizes, allowing for the creation of intricate and streamlined boat designs. This flexibility enables boatbuilders to optimize the use of space, resulting in more comfortable and functional boat interiors.
Another significant advantage of marine composites is their resistance to fatigue and impact. These materials can withstand repetitive loading and absorb energy, making them ideal for use in high-performance boats. This ensures that boats built with marine composites can withstand the rigors of rough sea conditions and maintain their structural integrity over time.
Moreover, marine composites are also known for their eco-friendly characteristics. Compared to traditional boatbuilding materials, such as wood and steel, marine composites have a lower environmental impact. They require fewer natural resources for production and have a reduced carbon footprint. Additionally, they are recyclable, further contributing to sustainable boat construction practices.
In conclusion, composite materials have played a transformative role in modern boatbuilding. Their lightweight and durable properties, coupled with design flexibility and eco-friendliness, offer boat builders an innovative and superior option for constructing high-performance and sustainable vessels.
Innovations in Marine Composite Technology
In recent years, marine composite technology has witnessed significant advancements, leading to innovative solutions that further enhance the performance and sustainability of boats. These advancements have revolutionized the boatbuilding industry, offering a wide range of benefits for manufacturers and boat owners alike.
Nanocomposites for Enhanced Performance
Delve into the realm of nanocomposites and discover their transformative role in marine engineering. These microscopic wonders are revolutionizing marine composite innovations, offering unprecedented strength and stiffness while minimizing damage susceptibility. Their high performance-to-weight ratio is paving the way for lighter, faster, and more efficient vessels, thereby elevating maritime operation standards and achieving new records in marine exploration and transportation.
Developments in Eco-friendly Marine Composites
The urgency for environmental stewardship has catalyzed the development of eco-friendly marine composites. Today’s research and development focus heavily on sustainable marine materials that not only perform admirably but also conscientiously respect our planet’s delicate ecosystems. Innovators are tirelessly working to formulate green boatbuilding solutions, such as easily recyclable composites and those derived from renewable resources. These materials promise a harmonious balance between high-performance marine crafts and the unwavering commitment to environmental conservation.
Marine Composite vs. Traditional Boatbuilding Materials
When it comes to boatbuilding, the choice of materials plays a crucial role in determining the vessel’s performance, durability, and overall cost-effectiveness. Marine composites have emerged as a game-changer in this industry, outperforming traditional materials like wood and steel in several key aspects.
Comparison with Wood and Steel
Considering wood versus composite, marine composites triumph with a multitude of benefits, including a notable strength-to-weight ratio that significantly surpasses that of wood. This advantage is not only a matter of structural integrity but also translates directly into enhanced efficiency and handling of marine vessels. In the debate of steel vs composite, steel, while known for its sturdiness, falls short due to its propensity to corrode in salty marine environments – an issue marine composites are engineered to resist. The comparison underscores the marked resilience of composite materials in face of the element’s wear and tear, establishing them as the progressive choice for nautical ventures.
Long-term Cost Savings Analysis
Marine material comparison extends beyond the physical attributes to consider the economic implications. Initial investments into marine composites may be higher, yet a detailed cost analysis reveals the shrewdness of this choice. Over time, the reduced need for maintenance, coupled with fewer repair requirements, presents significant long-term cost savings for owners. Furthermore, the enhanced operational efficiency of composite-built vessels underscores the belief that when it comes to the economy of scaling the seas, marine composites are the superior option. They justify their upfront costs, leading to accrued savings throughout a marine vessel’s lifecycle.