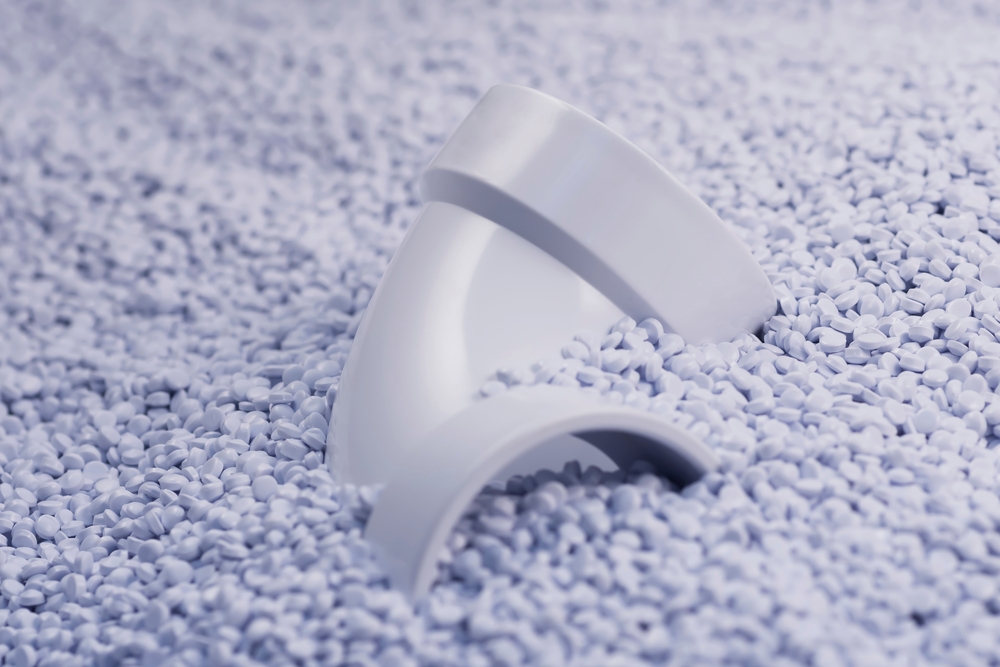
Engineering Plastics
Engineering plastics have emerged as a game-changing solution in modern manufacturing, offering a range of benefits over traditional materials. These high-performance materials have become indispensable in various industries, thanks to advancements in production techniques that have enhanced their properties.
Compared to traditional materials, they provide significant advantages. They are lighter, more flexible, and boast excellent mechanical properties. Moreover, they exhibit better chemical resistance and can withstand extreme temperatures.
The Role of Engineering Plastics in Modern Manufacturing
With the march of time, the manufacturing landscape has continually evolved, embracing materials that advance the intersection of innovation and functionality. Engineering plastics have surged to the forefront of this evolution, becoming stalwarts in material engineering and sustainable production. Their unique characteristics have ushered in a renaissance of manufacturing methodologies that challenge the very concepts of design and efficiency.
Advancements in Production Techniques
Historically, production techniques were limited by the capabilities of traditional materials, but the advent of manufacturing innovation has rewritten the playbook. High-strength plastics are now being manipulated through precision molding and cutting-edge extrusion processes, allowing for the creation of intricately detailed and complex components with unparalleled accuracy. These breakthroughs in material engineering not only expand the horizons of what can be built but also dramatically streamline the manufacturing process.
Engineering Plastics vs Traditional Materials
When juxtaposed with their traditional counterparts, the advantages of engineering plastics become exceedingly clear. They stand out with a formidable weight-to-strength ratio—an attribute highly sought after by manufacturers aiming for lightweight yet durable products. Sustainable production also becomes a tangible goal with engineering plastics, as they minimize the environmental footprint compared to the extraction, processing, and disposal associated with materials like metals and wood. Moreover, features like corrosion resistance and a reduced need for maintenance are revolutionizing product life cycles, leading to smarter, more resilient developments in a myriad of industries.
Types of Engineering Plastics and Their Properties
There are various types of engineering plastics available, each with its unique set of properties and characteristics. Some common types of engineering plastics include polyethylene, polypropylene, polycarbonate, ABS (Acrylonitrile Butadiene Styrene), and PEEK (PolyEtherEtherKetone).
Polyethylene is known for its high chemical resistance, low friction, and excellent electrical insulation properties. It is widely used in applications requiring corrosion resistance and electrical conductivity.
Polypropylene offers high stiffness, good impact resistance, and high thermal resistance. It is commonly used in the automotive industry for manufacturing parts such as bumpers and interior trims.
Polycarbonate is a tough and transparent plastic with excellent impact resistance and high heat resistance. It is often used in applications that require optical clarity and durability, such as lenses, safety goggles, and electronic device screens.
ABS is a versatile engineering plastic that combines the strength and rigidity of acrylonitrile and styrene with the toughness of polybutadiene. It is widely used in the automotive industry, consumer goods, and electronics for its excellent impact resistance and dimensional stability.
PEEK is a high-performance thermoplastic that exhibits exceptional mechanical properties, chemical resistance, and heat resistance. It is commonly used in aerospace, automotive, and medical applications where high strength, temperature resistance, and chemical compatibility are required.
Application Areas of Engineering Plastics
They have found extensive applications across various industries, owing to their versatile properties and exceptional performance characteristics. Let’s explore some of the key application areas where these advanced materials play a crucial role:
Automotive Industry
In the automotive industry, engineering plastics are widely used in the manufacturing of various components such as bumpers, interior trims, and engine parts. These plastics contribute to weight reduction, improved fuel efficiency, and enhanced safety in vehicles. By replacing traditional metal parts with lightweight engineering plastics, manufacturers can achieve significant weight savings without compromising strength or durability.
Electronics and Electrical Components
The electronics and electrical component sector greatly benefits from their use as well. Possessing excellent electrical insulation properties and resistance to heat and chemicals, they are ideal for producing connectors, insulating materials, and enclosures. By utilizing them in electronic devices, manufacturers can ensure the safety and longevity of electrical components while maintaining optimal performance.
Aerospace and Defense Applications
In the aerospace and defense sectors, they play a crucial role in manufacturing lightweight components that meet stringent safety and performance requirements. Extensively used in aircraft interiors, structural parts, and defense equipment, the incorporation of these materials can achieve weight reduction, fuel efficiency, and improved maneuverability without compromising strength or durability.
Overall, they have revolutionized various industries by providing innovative solutions to complex engineering challenges. Their exceptional properties, such as lightweight, strength, durability, chemical resistance, and heat resistance, make them invaluable in automotive, electronics, and aerospace sectors.
Advantages of Using Engineering Plastics
Using engineering plastics offers several advantages in various applications and industries. One of the primary advantages is improved durability and lifespan. Engineering plastics are designed to withstand harsh environments, extreme temperatures, and chemical exposure without degrading or breaking down easily. This makes them highly reliable and long-lasting materials for a wide range of applications.
Additionally, engineering plastics possess enhanced performance characteristics that contribute to their superiority over traditional materials. These plastics have high strength, stiffness, and toughness, allowing them to withstand heavy loads and resist deformation. They also exhibit excellent mechanical properties, including resistance to impact and fatigue.
Another significant advantage is their cost-effectiveness over time. While the initial cost may be higher compared to traditional materials, their longevity, reduced maintenance, and improved performance contribute to long-term savings. These materials require less frequent replacement, reducing downtime and expenses associated with repairs or replacements. Furthermore, their exceptional performance characteristics often enable manufacturers to design lighter and more efficient products, resulting in fuel savings and increased energy efficiency.
Improved Durability and Lifespan
Engineering plastics excel in their resistance to wear and teár, which significantly enhances the longevity of products. Long-lasting materials are intrinsic to engineering plastics, which repel the common agents of deterioration such as abrasion, fatigue, and environmental stressors. This robustness translates into tangible economic benefits through reductions in the frequency of replacements and maintenance operations.
Enhanced Performance Characteristics
Performance is paramount, and engineering plastics deliver remarkably. With their superior thermal resistance and impressive strength-to-weight ratios, these advanced materials provide a high-performance alternative that can easily be tailored to meet the demands of specific applications. The design flexibility inherent in engineering plastics further underscores their capacity to be shaped and adapted for a myriad of uses.
Cost-Effectiveness Over Time
An analysis of the full life cycle costs underscores the economic advantages of engineering plastics. Over time, the initial investment in these innovative materials yields returns through elongated service life and diminished energy requirements during both the production and usage phases of products. The confluence of extended durability, performance efficiency, and lower energy consumption positions engineering plastics as a cost-effective choice for long-term applications.
Innovations in the Field of Engineering Plastics
Ongoing innovations in the field of engineering plastics are driving the development of advanced materials with exciting new properties and capabilities. These innovations are revolutionizing industries and opening up new possibilities for designers, engineers, and manufacturers.
Smart Materials and Self-Healing Plastics
One of the more exhilarating developments in material science is the conception of smart engineering plastics. These materials are designed to react to changes in their environment, enabling products to adapt in real-time to temperature, pressure, and other external stimuli. Coupled with self-healing materials—plastics that intuitively repair themselves when compromised—the implications for durability and product lifespan are substantial. This industrial innovation extends the utility of products ranging from complex automotive components to everyday consumer electronics, potentially transforming maintenance norms across numerous industries.
3D Printing and the Maker Movement
Further driving the expansion of engineering plastics is the integration of 3D printing technology within the manufacturing sector. With its roots in the maker movement, 3D printing has matured into an industrial force, empowering designers and engineers to produce complex parts with a precision and speed previously unattainable. They are particularly amenable to this technology, thanks to their versatility and strength. As a result, customized production and rapid prototyping have become more accessible, fostering a new era of innovation and industrial agility. As industry leaders continue their investment in research and development, the potential for novel applications and enhanced material capabilities seems boundless.